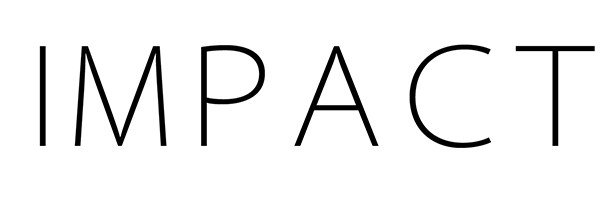
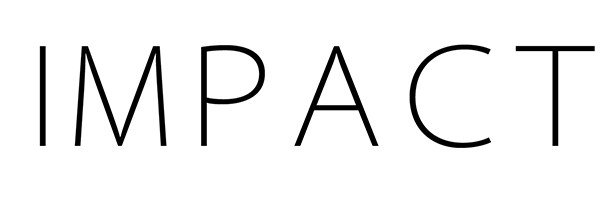
The collaborative research project IMPACT with a duration of 46 months (October 2019 - August 2023), was implemented in the framework of the Specific Action "Aquaculture - Industrial Materials - Open Innovation in Culture" and more specifically in Intervention Area 1. 16: Industrial materials of upgraded performance and the Thematic Area 1.16.4: Development of materials for particularly demanding environments of use in construction and industry (e.g. high corrosion, chemical attack, temperature, etc.), inorganic and organic materials: indicative materials: fire resistant, refractory materials).
The project focused on the development of improved materials based on the industrial mineral olivine with a twofold objective:
(i) increase mass refractoriness for applications in the steel industry; and
(ii) the replacement of silica silicon oxide in foundry sand with a more environmentally friendly raw material.
The challenges motivating IMPACT's research activities were associated with the need to develop industrial refractories and refractory materials able to perform under highly demanding environments and at the same time meet the continuous requirement of using friendlier materials, both for the environment and for people working in the industry. Therefore, the possibility of substituting conventional materials (such as magnesia and silica quartz sand) with olivine was explored.
In addition to investigating the materials on a laboratory scale, the project also evaluated the developed materials on an industrial scale, leading to the following conclusions:
The use of olivine as a protective coating for magnesite refractory bricks on electric arc furnaces in a steelworks showed that
Olivine can be used successfully
The use of olivine (with a phenolic resin binder) in mould casting has led to:
The project was implemented under the coordination of the industrial partner VITRUVIT. The project consortium included two research institutions of the Centre for Research and Technology Hellas (CERTH): the Institute of Chemical Processes & Energy Resources (CPERI) and the Institute of applied biosciences (INAB) and a second industrial partner, the company Gougoustamos D. Ltd (STAL).
Top left image: EAF furnace pre-firing works
Bottom left image: Mineral olivine
Right image: Metal casting operations and signage related to the risk from suspended SiO2 dust